Специальность:2-36 01 01-01 «Технология машиностроения 3 страница
| (22) [2], т. 9, стр. 271
| где – показатель степени;
= 0, 75
| [2], т. 9, стр. 271
|
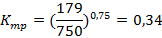
| [2], т. 23, стр. 275
|


2. 8 Определяем мощность резания. Проверяем, достаточна ли мощность привода станка:
| (23)
| где, – сила резания, Н;
– скорость главного движения резания, ;

КП 2021 2-36 01 01-01 06 01 П3
| Проверяем, достаточна ли мощность привода станка. Необходимо выполнение условия . У станка ГС526У

где – мощность двигателя станка, кВт;
– коэффициент полезного действия станка.

Таким образом, (4, 8 кВт ≤ 4, 9 кВт), значит, обработка возможна.
3 Определяем основное время:

где – количество проходов;
– длина рабочего хода резца, мм.
| (26)
| =1…3мм, принимаем
| (27)
|

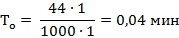
Операция 020 Вертикально-фрезерная
На вертикально-фрезерном станке 6Р12фрезеруется квадрат размером 55× 55мм.
Материал заготовки – 12Х18Н10Т
Приспособление – УДГ.
1Выбираем режущий инструмент и устанавливаем его геометрические параметры:
Принимаем концевую фрезу. Материал режущей части— быстрорежущая сталь Р6М5
D=40мм, z=6 зубьев
2 Определяем глубину резания:
t = b=40 мм
B=h=10мм
3 Определяем подачу:
= 0, 08…0, 05 мм/об [4, т. 35, стр. 284]
Принимаем =0, 05 мм/об
4 Определяем период стойкости фрезы:
Т = 120 мин [4, т. 40, стр. 290]
5 Определяем скорость главного движения резания:
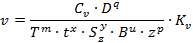
; [4, т. 4, стр. 263]
; [4, т. 6, стр. 263]
; [4, т. 31, стр. 280]
; q = 0, 35; y = 0, 48; m = 0, 27; x = 0, 21; u = 0, 03; p = 0, 1; [4, табл. 39, с. 287]
КП 2021 2-36 01 01-01 06 01 П3
| 6 Определяем частоту вращения шпинделя:

Корректируем по паспорту станка 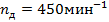
7Определяем действительную скорость главного движения резания:

8)Определяем скорость движения подачи:
Корректируем по паспортным данным станка
9) Определяем мощность затрачиваемую на резания:

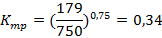
; q = 0, 86; y = 0, 6; x = 0, 75; u = 1; w= 0

КП 2021 2-36 01 01-01 06 01 П3
| 10) Проверяем, достаточна ли мощность станка:

кВт

Обработка возможна
11) Определяем основное время:
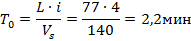
L = l+Δ +y=55+2+20 = 77 мм
где Δ = 1…3 мм, принимаем Δ = 2 мм;
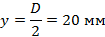
КП 2021 2-36 01 01-01 06 01 П3
| Таблица 10 – Сводная таблица режимов резания
Номер операции и модель станка
| Содержание перехода
| Номер инструмента
| D или В, мм
| t, мм
| Lрез, мм
| Lр. х. , мм
| i
| Подача
| n, мин-1
| V, мм/мин
| T0, мин
| S0, мм/об
| Sm, мм/мин
|
|
|
|
|
|
|
|
|
|
|
|
|
| 010 Токарно-винторезная
ГС526У
| 1. Подрезать торец в размер142 мм.
|
|
|
|
|
|
|
| 62, 5
|
|
| 0, 04
| 2. Точить Ø 78f9 мм на длину 71 мм.
|
|
|
|
|
|
| 0, 5
|
|
|
| 0, 24
| 3. Точить Ø 65k6 мм на длину 53, 5 мм
|
|
| 1, 85
| 53, 5
| 57, 5
|
| 0, 5
|
|
|
| 0, 64
| 4. Точить Ø 64 мм на длину 35 мм, Ra 6, 3
|
|
|
|
|
|
| 0, 5
|
|
|
| 0, 04
| 5. Точить канавку Ø 61, 8 на ширину 4 мм с радиусными закруглениями R1 и R0, 5 под углом 45º
|
|
| 2, 2
|
|
|
| 0, 3
|
|
|
| 0, 05
|
КП 2021 2-36 01 01-01 06 01 П3
| Продолжение таблицы 10
|
|
|
|
|
|
|
|
|
|
|
|
|
| 6. Точить фаску 2, 5× 45º
|
|
| 2, 5
| 2, 5
| 6, 5
|
| 0, 11
| 137, 5
|
|
| 0, 05
|
| 7. Нарезать резьбу М64× 1, 5-6g на длину 35
|
|
| 0, 37
|
|
|
| 1, 5
|
|
|
| 0, 07
| 8. Центровать
|
|
|
|
|
|
| 0, 1
|
|
|
| 0, 16
| 9. Сверлить Ø 42 на длину 142 мм
|
|
|
|
|
|
| 0, 8
|
|
|
| 2, 44
| 10. Расточить отверстие Ø 50, 5 на длину 60мм Ra 6, 3
|
|
| 1, 7
|
|
|
| 0, 5
|
|
|
| 0, 32
| 11. Точить канавку Ø 52, 7 шириной 6 мм с радиусными закруглениями R1, 6 и R1 под углом 45º
|
| 50, 5
| 2, 2
|
|
|
| 0, 3
|
|
|
| 0, 06
| 12. Точить фаску 1, 6× 45º
|
|
| 1, 33
| 1, 6
| 4, 93
|
| 1, 3
| 81, 9
|
| 10, 7
| 0, 06
| 13. Нарезать резьбу М52× 1, 5-6Н на длину 60
|
| 50, 5
| 0, 375
|
|
|
| 1, 5
|
|
|
| 0, 12
| 14. Точить фаску 1× 45º
|
|
|
|
|
|
| 0, 11
|
|
|
| 0, 05
| 015 Токарно-винторезная
ГС526У
| 1. Подрезать торец 2 мм
|
|
|
|
|
|
| 0, 5
| 62, 5
|
| 30, 8
| 0, 7
| 2. Точить Ø 73 на длину 70, 5 мм
|
|
| 1, 4
| 70, 5
| 74, 5
|
| 0, 5
|
|
|
| 0, 6
| 3. Точить Ø 52 на длину 33 мм, Ra 6. 3
|
|
| 1. 84
|
|
|
| 0. 5
|
|
|
| 0, 36
| 4. Точить 2 фаски 2, 5× 45º
|
|
| 2, 5
| 2, 5
| 6, 5
|
| 0, 11
|
|
|
| 0, 04
|
| | Продолжение таблицы 10
|
|
|
|
|
|
|
|
|
|
|
|
|
| 5. Точить канавку Ø 49, 8 шириной 4 мм с радиусными закруглениями R1 и R0, 5 под углом 45º
|
|
| 2, 2
|
|
|
| 0, 3
|
|
|
| 0, 04
| 6. Нарезать резьбу М52× 1, 5-6g на длину 33
|
|
| 1, 5
|
|
|
| 1, 5
|
|
|
| 0, 07
| 7. Точить фаску 1× 45º
|
|
|
|
|
|
| 0, 11
|
|
|
| 0, 05
| 020 Вертикально-фрезерная 6Р12
| 1. Фрезеровать квадрат 55× 55
|
|
|
|
|
|
| 0, 05
| 22, 5
|
| 58, 2
| 2, 2
| КП 2021 2-36 01 01-01 06 01 П3
|
КП 2021 2-36 01 01-01 06 01 П3
| 2. 4. 2 Нормирование проектируемой операции. Сводная таблица норм времени.
Операция 010Токарно-винторезная

где – вспомогательное время на обработку;
– основное время на обработку;
– время на обслуживание и отдых;
То = 4, 34 мин.

где – время на установку и снятие инструмента, мин;
– время на закрепление и открепление заготовки или изделия, мин;
– время управления оборудованием, мин;
– время на измерение заготовки или изделия, мин.
= 0, 23мин; [6 т. A1, cтр. 304]
= 0, 094мин; [6т. A7, cтр. 311]
= 0, 02 + 0, 02 + 0, 025 = 0, 065мин; [6т. A8, cтр. 312]
=0, 16мин. [6т. A16, cтр. 320]


КП 2021 2-36 01 01-01 06 01 П3
| Топ – оперативное время на обслуживание, мин;
Побот = 6, 5% [т. Б1, стр. 330]


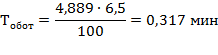


где - подготовительно-заключительное время;
n- количество деталей в партии;
- штучное время.
Тп. з. =12 [т. Б3, с. 332]

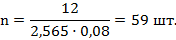

Таблица 11. 2 – Сводная таблица норм времени
Номер операции и модель станка
|
|
|
|
|
|
|
|
|
| n шт
|
| 010 Токарно-винторезная
ГС526У
| 4, 34
| 0, 23
| 0, 094
| 0, 065
| 0, 16
| 4, 889
| 0, 317
| 5, 206
|
|
| 5, 409
| 015 Токарно-винторезная
ГС526У
| 1, 86
| 0, 23
| 0, 094
| 0, 065
| 0, 16
| 2, 409
| 0, 156
| 2, 565
|
| 2, 768
|
Вертикально-фрезерная
6Р12
| 2, 2
| 0, 053
| 0, 153
| 0, 34
| 0, 16
| 2, 906
| 0, 232
| 3, 138
|
| 3, 46
| КП 2021 2-36 01 01-0106 01 П3
|
КП 2021 2-36 01 01-0106 01 П3
| Заключение
При разработке технологического процесса изготовления детали типа “Втулка” были учтены особенности серийного производства, а именно – оптимальный выбор получения заготовки – прокат, что позволяет снизить себестоимость изготовления детали.
В проектном технологическом процессе по сравнению с базовым технологическим процессом увеличилось потребление электроэнергии за счёт увеличения общей активной мощности станков. Также был заменен токарно-винторезный станок 16К20 на токарно-винторезный станок ГС526У, который имеет наиболее высокую точность.
При выполнении курсового проекта были получены и закреплены сведения о составлении технологического процесса, принципах выбора оборудования и инструмента, аналитическом расчёте припусков, режимов резания и технического нормирования, что в условиях серийного производства является крайне важным.
Содержание
Введение 4
1 Анализ исходных данных 5
1. 1 Описание конструкции и служебного назначения детали 5
1. 2 Описание типа производств и его характеристик 6
1. 3 Анализ детали на технологичность 7
2 Разработка технологии обработки детали 9
2. 1 Анализ технических требований, предъявляемых к детали. Рекомендации по их обеспечению и контролю 9
2. 2. Выбор вида и обоснования метода получения заготовки. Описание метода получения заготовки 9
2. 2. 1 Определение припусков на механическую обработку поверхностей по переходам 11
2. 3 Разработка проектного технологического процесса 15
2. 3. 1 Анализ базового технологического процесса и составление последовательности обработки для проектируемого технологического процесса 15
2. 3. 2 Выбор и обоснование технологических баз 17
2. 3. 3 Выбор оборудования и технологической оснастки 19
2. 4 Разработка операционного технологического процесса 21
2. 4. 1 Определение режимов резания на проектируемые операции. Сводная таблица режимов резания 21
2. 4. 2 Нормирование проектируемых операций. Сводная таблица норм времени 28
3 Мероприятия по энерго- и ресурсосбережению 30
Заключение 31
Литература 32
Графическая часть курсового проекта:
1 Чертёж детали
2 Чертёж заготовки
3-4 Операционные эскизы на две разнохарактерные операции
5 Комплект технологической документации
|
|
|
|
| КП 2022 2-36 01 01-01 06. 01 ПЗ
|
|
|
|
|
| Изм.
| Лист
| № докум
| Подпись
| Дата
| Разраб
| Кузьмичёв
|
|
| Разработка технологического процесса механической обработки детали типа «Втулка»
Пояснительная записка
| Литера
| Лист
| Листов
| Пров
| Лабохо М. В.
|
|
|
| y
|
|
|
|
|
|
|
| гр. 19-ДБМ
| Н. Контр.
|
|
|
| Утв
|
|
|
| | | | | | | | | | | |
|
|