Специальность:2-36 01 01-01 «Технология машиностроения 2 страница
0
=110 [1], т. 38, стр. 80
0
ε =110 мкм
Для чернового точения погрешность установки определяется:


Для чистового точения погрешность установки определяется:


КП 2021 2-36 01 01-01 06 01 П3
| 2. Выбираем формулу для расчёта величины припуска на обработку:
где: Rz – высота неровностей, мкм;
Т – глубина дефектного слоя, мкм;
P – суммарное значение пространственных отклонений, мкм;
i-1 – значение для предыдущего перехода
i – текущий переход.
Для чернового точения расчётный припуск:
)= 832, 7 мкм
Для чистового точения расчётный припуск
)= 201, 9мкм
3 Определяем расчетный размер. Графа «расчётный размер» заполняется, начиная с конечного размера путём последовательного прибавления расчётного припуска каждого перехода:
мм
мм
мм
4 Определяем допуски с чертежа. Допуски на последующие переходыберутся из таблицы допусков, через квалитет.
=1, 9 мм
мкм= 1, 2 мм
= 0, 74 мм
5 Определяем предельные размеры. Минимальные предельные размеры равны расчётным размерам :
= 73 мм
= 73, 2019 мм
= 74, 0346 мм
Наибольшие предельные размеры определяются путём прибавления к наименьшим предельным размерам допусков соответствующего перехода.

КП 2021 2-36 01 01-01 06 01 П3
|

мм

мм

мм
6Определяем предельные значения припусков. Предельные значения припусков определяем как разность наибольших предельных размеров предшествующего и выполняемого переходов:
= 



Предельные значения припусков определяем как разность наименьших предельных размеров предшествующего и выполняемого переходов:




7 Проводим проверку правильности выполнения расчётов:


Условие проверки выполняется


Условие проверки выполняется КП 2021 2-36 01 01-01 06 01 П3
|
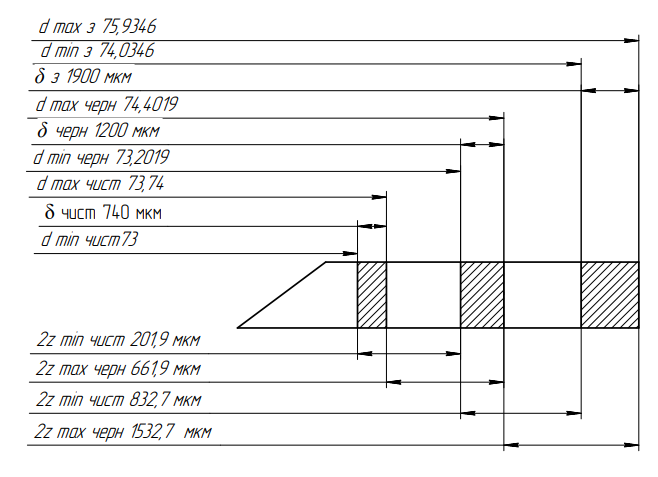
Рисунок 2 - Схема графического расположения припусков на обработку поверхности 73 мм.
2. 3 Разработка проектного технологического процесса
2. 3. 1 Анализ базового технологического процесса и составление последовательности обработки для проектируемого технологического процесса
В базовом технологическом процессе, точение детали типа «Втулка» производилось на токарном станке ГС526У. Предназначение данного станка рационально,
Так как станок обладает высокой точностью и позволит обработать сложные поверхности с высокой точностью. Станок обеспечит быстродействие обработки, высокое качество изделий, стабильность размеров. Высокая жёсткость конструкции, большая мощность привода главного движения, широкий диапазон подач и частот вращения шпинделя позволяет вести точение с большим припуском без потери точности с применением современного инструмента.
КП 2021 2-36 01 01-01 06 01 П3
| Таблица 2. 3 - Технологический процесс изготовления детали «Втулка»
№
операции
|
Наименование операции
|
Эскиз
| Оборудование, режущий и мерительный инструмент
|
|
|
|
|
| Ножовочно-отрезная
1)Отрезать заготовку в размер
|
| Ножовочно-отрезной станок 8725
1)Режущее полотно;
2)ШЦ
|
| Токарно-винторезная
1) Подрезать торец в размер 142 мм
2) Точить
3) Точить
4) Точить , Ra 6, 3
5) Точить канавку шириной 4 с радиусными закруглениями R1 и R0, 5 под углом 45º
6) Точить фаску
7) Нарезать резьбу М64 × 1, 52 - 6g на длину 35
8) Центровать отверстие
9) Сверлить
10) Расточить отверстие , Ra 6, 3
11) Точить канавку шириной 6 с радиусными закруглениями R1, 6 и R1 под углом 45º
12) Зенковать фаску 1, 6× 45º
13) Нарезать резьбу М52 × 1, 5 - 6H на длину 60
14) Точить фаску 1× 45º
|
| Токарно-винторезный станок ГС526У
1)Проходной отогнутый резец
2)Проходной упорный резец
3)Канавочный резец
4)Сверло спиральное
5)Расточной резец
6)ШЦ
7)Цетровочное сверлло
8)Резьбонарезной резец
9) Микрометр
10)Шаблон
|
Продолжение таблицы 2. 3
| Токарно-винторезная
1)Подрезать торец в размер 140
2)Точить
3)Точить , Ra 6, 3
4)Точить 2 фаски 2, 5× 45º
5) Точить канавку шириной 4 с радиусными закруглениями R1и R0, 5 под углом 45º
6) Нарезать резьбу М52 × 1, 52-6g на длину 33
7) Точить фаску 1× 45º
|
| Токарно-винторезный станок ГС526У
1)Проходной отогнутый резец
2)Проходной упорный резец
3)Канавочный резец
4)Резьбонарезной резец
5)ШЦ
| 020
| Вертикально-фрезерная
1) Фрезеровать квадрат 55 × 55
|
| Вертикально-фрезерный станок 6Р12
1)Концевая фреза
2)ЩЦ
|
КП 2021 2-36 01 01-01 06 01 П3
|
2. 3. 2 Выбор и обоснование технологических баз
Схемы базирования и закрепления, технологические базы, опорные и зажимные элементы, устройства и приспособления должны обеспечивать определенное положение заготовки относительно режущего инструмента, надежность ее закрепления и неизменность базирования в течение всего процесса обработки.
Поверхности заготовки, принятые в качестве баз и их относительное расположение должны быть такие, чтобы можно было использовать наиболее простую и надежную конструкцию приспособления, удобство установки, закрепления, открепления и снятия заготовки, возможность приложения в нужных местах сил зажима и подвода режущего инструмента.
При выборе баз следует учитывать основные принципы базирования, при этом необходимо руководствоваться следующими соображениями:
В качестве чистовых технологических баз принимать те элементы детали, которые являются базами конструкторскими и измерительными, что уменьшает погрешность базирования, так как выполняется принцип совмещения баз;
КП 2021 2-36 01 01-01 06 01 П3
| Строить обработку таким образом, чтобы чистовые технологические базы были одними и теми же на протяжении всего технологического процесса, что обеспечивает выполнение принципа постоянства баз;
Смену чистовых баз производить в том случае, если необходимо выполнить принцип совмещения баз для обеспечения нулевой погрешности базирования;
В качестве черновых баз на первых операциях назначать те элементы, относительно которых обрабатываются будущие чистовые базы, и использовать черновые базы только один раз.
В качестве основных баз при обработке используются: наружная поверхность; +торцы детали;
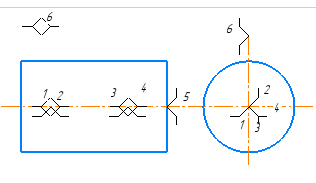
Операция 010Токарно-винторезная
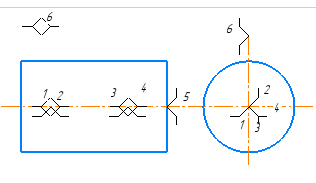
Операция 015 Токарно-винторезная
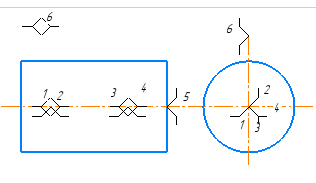
Операция 020 Вертикально-фрезерная
2. 3. 3 Выбор оборудования и технологической оснастки
Таблица 2. 4– Выбор оборудования
Номер операции
| Модель станка
| Наименование станка
| Действительный фонд времени работы оборудования в зависимости от категории ремонтной сложности
| Стоимость станка, руб.
| Паспортные данные
| Размеры посадочных элементов станка, мм
| Предельные размеры обрабатываемых заготовок, мм
| Габаритные размеры станка, мм
| Вид и мощность привода главного движения, кВт
| Ряд частот, мин-1
| Ряд подач, мм/об или мм/мин
|
|
|
|
|
|
|
|
|
|
|
|
|
| Ножовочно-отрезной
|
|
| Ножовочное полотно
| 140× 250 мм
| 1450× 900× 1060
| 2, 2
| 20-1600
| 85-110
|
| ГС526У
| Токарно-винторезный
|
|
| Конус Морзе 5
| Ø 350× 530 мм
| 2800× 1265× 1485
| 7, 5
| 16-2000
| 0, 025-1, 4
|
| 6Р12
| Вертикально-фрезерный
|
|
| Конус Морзе 3
| 450× 650 мм
| 2280× 1965× 2265
| 7, 5
| 40-2000
| 0, 1-0, 6
| КП 2021 2-36 01 01-01 06 01 П3
|
Таблица 2. 5 – Выбор установочно-зажимных приспособлений
Номер операции и модель станка
| Приспособление
| Код
| Наимено- вание
| Тип привода
| Технические характеристики
| Обозначение по стандарту
|
|
|
|
|
|
| 010-015 ГС526У
|
| Трёхкулач- ковый патрон
| Ручной
| ⌀ 150
| ГОСТ 2675-80
| 020 6Р12
|
| Удг
| Ручной
| ⌀ 320
| ГОСТ 8615-89
|
Таблица 2. 6 – Выбор режущего инструмента
Номер операции и модель станка
| Режущий инструмент
| Код и наимено- вание режущего инструмента
| Материал режущего инструмента
| Технические характеристики, мм
| Обозначение по стандарту
| Применяемая технологическая смесь
|
|
|
|
|
|
| 005 8725
| Ножовочное полотно 392540
| Р6М5
|
| ГОСТ 6645-86
| Кармабод П-1
| 010-015 ГС526У
| Проходной упорный резец 392110
| Р18
| 16× 25× 80
| ГОСТ 18879-73
| Эмульсод СП-3
| Расточной резец 392110
| Р18
| 16× 16× 170
| ГОСТ 18883-73
| Эмульсод СП-3
| Сверло спиральное 391267
| Р6М5
| ⌀ 42
| ГОСТ 10903-77
| Эмульсод СП-3
| Проходной
отогнутый резец
| Р18
|
|
| Эмульсод СП-3
| Канавочный
резец
| Р18
|
|
| Эмульсод СП-3
| Центровочное
сверло
| Р6М5
|
|
| Эмульсод СП-3
| Резьбонарезной резец
| Р18
|
|
| Эмульсод СП-3
| Зенковка
| Р9
|
|
| Эмульсод СП-3
|
6Р12
| Концевая
фреза
| Р6М5
|
|
| Эмульсод СП-3
|
КП 2021 2-36 01 01-01 06 01 П3
| 2. 4 Разработка операционного технологического процесса
2. 4. 1 Определение режимов резания на проектируемые операции (переходы). Сводная таблица режимов резания
Операция 010 Токарно-винторезная
На токарно-винторезном станке ГС526Уподрезается торец диаметром D = 80 мм.
Материал заготовки – 12Х18Н10Т
Приспособление – трёхкулачковый самоцентрирующийся патрон.
1) Выбираем режущий инструмент:
Принимаем токарный проходной отогнутый резец. Материал рабочей части – пластины – Т15К6; материал корпуса резца – сталь 45.
Геометрические элементы резца φ = 45°; φ 1 = 45°; r = 1.
2 Назначаем режимы резания:
2. 1 Устанавливаем глубину резания:
2. 2 Определяем подачу:
S = 1 мм/об. [2], т. 11, стр. 266
|
|
КП 2022 2-36 01 01-01 13 01 П3
| 2. 3 Определяем период стойкости:
Т = 60 мин. [2], стр. 268
|
2. 4 Определяем скорость главного движения резания:
(16)[2], стр. 265
|
|
где , , , – коэффициенты;
– период стойкости, мин;
– глубина резания, мм;
– подача, мм/об;
– общий поправочный коэффициент;
= 340
= 0, 15
= 0, 45
= 0, 2
|
[2], т. 17, стр. 269
|
| (17)
|
где, – коэффициент влияния материала заготовки;
– коэффициент состояния поверхности;
– коэффициент материала инструмента;
[2], т. 3, стр. 262
[2], т. 5, стр. 263
[2], т. 6, стр. 263


2. 5 Определяем частоту вращения шпинделя:

где, – скорость главного движения резания, ;
– диаметр заготовки, мм;

КП 2021 2-36 01 01-01 06 01 П3
| Корректируем по паспортным данным станка:
| [4], с. 421
|
2. 6 Определяем действительную скорость резания:
| (19)
|
где, – скорректированная частота вращения шпинделя;

2. 7 Определяем силу, затрачиваемую на резание:
| (20)
|
где, – коэффициент, влияющий на силу, затрачиваемую на резание;
– показатели степени;
– глубина резания, мм;
– подача, ;
– скорость главного движения резания, ;
= 204;
= 1;
= 0, 75;
= 0;
| [2], т. 22, стр. 273
|
| (21)
|
где, – коэффициент, учитывающий влияние качества обрабатываемого материала на силовые зависимости;
– коэффициенты, учитывающие влияние геометрических параметров режущей части инструмента на составляющие силы резания.
|