Название дисциплины: «ОП.04 Материаловедение»
1. Название дисциплины: «ОП.04 Материаловедение»
2. Номер группы:ТОР 21-1Т
3. Форма и дата занятия: практическое занятие, 10.11.2021
4. ФИО преподавателя:Гумерова Сабарчан Шамсулеймановнаsoja1984renat@mail.ru,вк: 89526782142, https://vk.com/club207530304
5. Срок выполнения (сдачи) задания:10.11.2021г
Тема Пластмассы, антифрикционные, композитные материалы.
Практическая работа №8 Определение строения и свойств композитных материалов Задание.
1.Прочитать материал по теме. Составить краткий конспект, ответить на вопросы.
Теоретический материал
Композиционные материалы Композиты — многокомпонентные материалы, состоящие из полимерной, металлической, углеродной, керамической или другой основы (матрицы), армированной наполнителями из волокон, нитевидных кристаллов, тонкодиспeрсных частиц и др. Путем подбора состава и свойств наполнителя и матрицы (связующего), их соотношения, ориентации наполнителя можно получить материалы с требуемым сочетанием эксплуатационных и технологических свойств. Использование в одном материале нескольких матриц (полиматричные композиционные материалы) или наполнителей разл. природы (гибридные композиционные материалы) значительно расширяет возможности регулирования свойств композиционных материалов. Армирующие наполнители воспринимают основную долю нагрузки композиционных материалов.
По структуре наполнителя композиционные материалы подразделяют на волокнистые (армированы волокнами и нитевидными кристаллами), слоистые (армированы пленками, пластинками, слоистыми наполнителями), дисперсноармированные, или дисперсноупрочненные (с наполнителем в виде тонкодисперсных частиц).
Матрица в композиционных материалах обеспечивает монолитность материала, передачу и распределение напряжения в наполнителе, определяет тепло-, влаго-, огне- и химическую стойкость. По природе матричного материала различают полимерные, металлические, углеродные, керамические и другие композиты. Наиболее широкое применение в технике получили композиционные материалы, армированные высокопрочными и высокомодульными непрерывными волокнами.
К ним относят: полимерные композиционные материалы на основе термореактивных (эпоксидных, полиэфирных, феноло-формальдегидных, полиимидных и др.) и термопластичных связующих, армированных стеклянными (стеклопластики), углеродными (углепластики), орг. (органопластики), борными (боропластики) и другими волокнами; металлические композиционные материалы на основе сплавов Al, Mg, Cu, Ti, Ni, Сг, армированных борными, углеродными или карбидкремниевыми волокнами, а также стальной, молибденовой или вольфрамовой проволокой; композиционные материалы на основе углерода, армированного углеродными волокнами (углерод-углеродные материалы); композиционные материалы на основе керамики, армированной углеродными, карбидкремниевыми и другими жаростойкими волокнами и SiC.
При использовании углеродных, стеклянных, арамидных и борных волокон, содержащихся в материале в кол-ве 50-70%, созданы композиции с ударной прочностью и ударным модулем упругости в 2-5 раз большими, чем у обычных конструкционных материалов и сплавов. Кроме того, волокнистые композиционные материалы превосходят металлы и сплавы по усталостной прочности, термостойкости, виброустойчивости, шумопоглощению, ударной вязкости и другим свойствам.
Эпоксидные смолы и композиции на их основе Достоинствами эпоксидных смол являются их механическая прочность, химическая стойкость, высокие диэлектрические свойства после отверждения, малая усадка, прекрасная адгезия к металлам, стеклу, дереву и ряду других материалов. Эпоксидные смолы легко совмещаются со многими полимерами и олигомерами, что используется для изменения некоторых их свойств. Из модифицированных таким образом эпоксидных смол большой интерес представляют эпоксиднофенольные (повышенная термостойкость по сравнению с эпоксидными смолами, эпоксидно-полиэфирные (повышенная стойкость к ударным нагрузкам), эпоксидно-фурановые, эпоксидно-полиамидные и другие композиции.
В зависимости от свойств эпоксидные смолы применяется для получении слоистых пластиков, стеклопластиков, покрытий и т. д. Клеи на основе эпоксидных смол могут быть жидкими в виде порошка и прутков.
При использовании эпоксидных клеев склеиваемые поверхности нагревают до 120 град. С, посыпают порошком или затирают прутком. При этом клей плавится и растекается по поверхности. На основе эпоксидных смол изготовляют электроизоляционные компаунды горячего и холодного отверждения, которые представляют собой композиции эпоксидной смолы отвердителя наполнителя и пластификатора. Эти компаунды влагостойки и выдерживают длительное нагревание до 130 град.С.
Их применяют для заливки контурных катушек, трансформаторов, дросселей цементации витков катушек в электрических машинах, склеивания высоковольтных фарфоровых изоляторов, электроизоляции мест с оединения проводов и т. д. Наполнителями при получении компаундов служат волокнистые и порошкообразные материалы: стеклянные волокна, двуокись кремния и др.
В зависимости от допустимой температуры отверждения компаунда применяют различные отвердители, например, для отверждения при повышенной температуре можно использовать малеиновый ангидрид. Для отверждения компаундов при комнатной температуре обычно применяют первичные диамины и полиамины.
Эпоксидные смолы широко применяются для получения лакокрасочных покрытий, в этих случаях смола отверждается уже в виде нанесенной пленки. Кроме эпоксидиановых выпускаются эпоксидные смолы, получаемые взаимодействием эпихлоргидрина с резорцином, ароматическими моно- и диаминами (анилином и др.), а также с гликолями — так называемые алифатические эпоксидные смолы. Последние отличаются пониженной вязкостью, повышенной эластичностью в отвержденном состоянии и применяются преимущественно как разбавители эпоксидиановых смол.
Пенопласты — газонаполненные пластические массы ячеистой структуры. Пенопласты имеют строение отвердевших пен. Они содержат преимущественно замкнутые, не сообщающиеся между собой полости, разделённые прослойками полимера. Этим они отличаются от поропластов, пронизанных системой связанных каналов-пор, то есть имеющих губчатую структуру. Также пенопласты могут состоять из отдельных гранул (чаще всего пенополистирол).
Выделение пенопластов среди прочих газонаполненных пластмасс в отдельную классификационную группу по признаку изолированности ячеекполостей достаточно условно, так как во многих пеноматериалах значительная их часть всё же соединена. Правильнее к пенопластам относить любой газонаполненный полимер, полученный путём вспенивания и последующего отверждения первоначально жидкой или пластично-вязкой композиции.
При производстве пенопластов газ диспергируют в полимерном сырье полуфабрикате (растворе, расплаве, жидком олигомере, дисперсии) или создают условия для выделения газовой фазы непосредственно в объёме отверждаемого продукта.
Технология производства пенопластов бывает основана на различных технологических приёмах вспенивания: механическое перемешивание или барботирование в присутствии пенообразователей; введение газообразователей (веществ, разлагающихся с выделением газа) или веществ, взаимодействующих с образованием газообразных продуктов; насыщение исходной смеси газом под давлением с последующим снижением давления; введение жидкостей, быстро испаряющихся с повышением температуры.
В зависимости от состава композиции и условий её отверждения получают материал с преимущественно открытыми или замкнутыми ячейками. Соответственно оборудование для изготовления пенопластов подразделяется на классы в зависимости от характеристик полимерной основы пенопласта и способа получения вспененного материала.
Экструзионный (или экструдированный) пенопласт получают путем вспенивания полимера непосредственно в цилиндре и формующем инструменте экструдера. Изделия из пенополиуретана, как мягкого, так и жесткого, производители получают путем заливки в формы под давлением на специальных заливочных машинах ППУ.
При литье пенополиуретановых изделий используется технология смешения двух компонентов сырья – полиола и изоцианата. Вспененные материалы можно получать и на обычном оборудовании для переработки пластмасс – экструзионных линиях и термопластавтоматах путем использования специальных добавок к сырью, порофоров.
Изделия из пористых материалы можно изготавливать также вымыванием из монолитной полимерной заготовки растворимого наполнителя, спеканием порошкообразных полимерных материалов, путём конденсационного структурообразования в растворах полимеров. Близки по свойствам к пенопластам газонаполненные пластмассы, полученные с применением полых наполнителей, например заполненных газом сферических микрокапсул.
Пенопласты можно приготовить из большинства синтетических и многих природных полимеров. Однако пенопласты промышленного назначения выпускают главным образом на основе полистирола (ПС), полиэтилена (ПЭ), поливинилхлорида (ПВХ), полиуретанов (ПУ), полипропилена (ПП), фенольных, эпоксидных, карбамидных и кремнийорганических смол. В качестве газообразователей применяют азосоединения, нитросоединения, карбонат аммония и др.; из легкокипящих жидкостей — изопентан, метиленхлорид, фреоны.
Промышленность выпускает жёсткие и эластичные пенопласты с размером ячеек 0,02—2 мм (иногда до 3—5 мм). Они обладают чрезвычайно низкой кажущейся плотностью (0,02— 0,5 г/см2) и превосходными тепло- и звукоизоляционными свойствами. Водостойкость, механические и электрические характеристики пенопластов зависят от химической природы и рецептурного состава полимерной композиции, а также от особенностей структуры готового продукта. Изделия из пенопластов обычно не требуют последующей обработки, из чего следует что и количество отходов пенопласта обычно невысоко. Это говорит об экологичности процесса и делает его еще более привлекательным для производителей.
Пенопласты широко применяют в самолётостроении и судостроении, в транспортном и химическом машиностроении, в строительстве зданий и технических сооружений как листовой тепло- и звукоизоляционный материал. Полистирольный пенопласт используется и как отделочный материал в строительстве, из него делают различные декоративные плитки, панели, молдинги, плинтусы. Постоянно растущие продажи стройматериалов обеспечивают существенный рост выпуска различных пенопластов как в России, так и за рубежом.
Пенопласты используют при изготовлении многослойных конструкций, различных плавучих средств (понтонов, лёгких лодок, бакенов, спасательных поясов и др.). Теплопроводность пенопласта крайне мала – это одно из основных свойств, определяющих его применимость в различных областях науки и техники. Прозрачность пенопластов для радиоволн и достаточно высокие диэлектрические и гидроизоляционные свойства обеспечивают этим материалам применение в радиотехнике и электротехнике.
Пенопласты широко используются в технологии получения амортизирующих и демпфирующих прокладок, разнообразной тары и упаковки для оптических и других хрупких приборов и механизмов, электронной аппаратуры и др. изделий. Упаковочный пенопласт, как правило, представляет собой отформованный в соответствии с контурами упаковываемого продукта пенополистирольный материал. Огромный рынок эластичных пенопластов — производство мягкой мебели и тёплой одежды.
Стеклопластики Описание стеклопластиков Стеклопластик — композиционный материал, состоящий из стеклянного наполнителя и синтетического полимерного связующего. Наполнителем служат в основном стеклянные волокна в виде нитей, жгутов (роввингов), тканей, матов, рубленых волокон; связующим — полиэфирные, фенолоформальдегидные, эпоксидные, кремнийорганические смолы, полиимиды, алифатические полиамиды, поликарбонаты и др. Для стеклопластика характерно сочетание высоких прочностных, диэлектрических свойств, сравнительно низкой плотности и теплопроводности, высокой атмосферо-, водо- и химстойкости.
Механические свойства стеклопластика определяются преимущественно характеристиками наполнителя и прочностью связи его со связующим, а температуры переработки и эксплуатации — связующим. Наибольшей прочностью и жёсткостью обладают стеклопластики, содержащие ориентированно расположенные непрерывные волокна. Такие стеклопластики подразделяются на однонаправленные и перекрёстные; у первых волокна расположены взаимно параллельно, у вторых — под заданным углом друг к другу, постоянным или переменным по изделию. Изменяя ориентацию волокон, можно в широких пределах регулировать механические свойства стеклопластиков.
Большей изотропией механических свойств обладают стеклопластики с неориентированным расположением волокон: материалы на основе рубленых волокон, нанесённых на форму методом напыления одновременно со связующим, и на основе холстов (матов). Диэлектрическая проницаемость стеклопластиков 4-14, тангенс угла диэлектрических потерь 0,01-0,05.
Изделия из стеклопластика с ориентированным расположением волокон изготавливают методами намотки, послойной выкладки или протяжки с последующим автоклавным, вакуумным или контактным формованием либо прессованием, из пресс-материалов — прессованием и литьём.
Примеры изделий из стеклопластика Стеклопластик применяют как конструкционный и теплозащитный материал при производстве корпусов лодок, катеров, судов и ракетных двигателей, кузовов автомобилей, цистерн, рефрижераторов, радиопрозрачных обтекателей, лопастей вертолётов, выхлопных труб, деталей машин и приборов, коррозионностойкого оборудования и трубопроводов, небольших зданий, бассейнов для плавания и др., а также как электроизоляционный материал в электро- и радиотехнике.
Свойства стеклопластиков Стеклопластик обладает многими очень ценными свойствами, дающими ему право называться одним из материалов будущего. Ниже перечислены некоторые из них. Малый вес. Удельный вес стеклопластиков колеблется от 0,4 до 1,8 и в среднем составляет 1,1 г/см3. Напомним, что удельный вес металлов значительно выше, например, стали – 7,8, а меди — 8,9 г/см3. Даже удельный вес одного из наиболее легкого сплава, применяемого в технике, дуралюмина составляет 2,8 г/см3. Таким образом, удельный вес стеклопластика в среднем в пять-шесть раз меньше, чем у черных и цветных металлов, и в два раза меньше, чем у дуралюмина. Это делает стеклопластик особенно удобным для применения на транспорте. Экономия в весе на транспорте переходит в экономию энергии; кроме того, за счет уменьшения веса транспортных конструкций (самолетов, автомобилей, судов и т.п.) можно повысить их полезную нагрузку и за счет экономии топлива увеличить радиус действия.
Диэлектрические свойства. Стеклопластики являются прекрасными электроизоляционными материалам при использовании как переменного, так и постоянного тока.
Высокая коррозионная стойкость. Стеклопластики как диэлектрики совершенно не подвергаются электрохимической коррозии. Существует целый ряд смол (некоторые полиэфирные смолы, смолы Norpol DION), позволяющие получить стеклопластики стойкие к различным агрессивным средам, в том числе и к воздействию концентрированных кислот и щелочей.
Хороший внешний вид. Стеклопластики при изготовлении хорошо окрашиваются в любой цвет и при использовании стойких красителей могут сохранять его неограниченно долго.
Прозрачность. На основе некоторых марок светопрозрачных смол можно изготовить стеклопластики, по оптическим свойствам немногим уступающим стеклу.
Высокие механические свойства. При своем небольшом удельном весе стеклопластик обладает высокими физико-механическими характеристиками. Используя некоторые смолы, например Norpol Dion, и определенные виды армирующих материалов, можно получить стеклопластик, по своим прочностным свойствам превосходящий некоторые сплавы цветных металлов и стали.
Теплоизоляционные свойства. Стеклопластик относится к материалам с низкой теплопроводностью. Кроме того, можно значительно повысить теплоизоляционные свойства путем изготовления стеклопластиковой конструкции типа “сэндвич”, используя между слоями стеклопластика пористые материалы, например пенопласт. Благодаря своей низкой теплопроводности, стеклопластиковые сэндвичевые конструкции с успехом применяются в качестве теплоизоляционных материалов в промышленном строительстве, в судостроении, в вагоностроении и т.д.
Простота в изготовлении. Существует много способов изготовления стеклопластиковых изделий, большинство из которых требует минимальных вложений в оборудование. Например, для ручного формования потребуются только матрица и небольшой набор ручных инструментов (прикаточные валики, кисти, мерные сосуды и т.д.). Матрица может быть изготовлена практически из любого материала, начиная с дерева и заканчивая металлом. В настоящие время широкое распространение получили стеклопластиковые матрицы, которые имеют сравнительно небольшую стоимость и длительный срок службы.
Производство стеклопластиков Стеклопластик получают путем горячего прессования стекловолокна, перемешанного с синтетическими смолами. В стеклопластиках стекловолокно играет роль армирующего материала, придающего изделиям высокую механическую прочность при малой плотности.
В настоящее время существует целый ряд различных смол, используемых в производстве стеклопластиковых изделий. Наибольшее распространение получили полиэфирные, винилэфирные и эпоксидные смолы.
В зависимости от метода формования, химсостава и области применения все смолы можно разделить на следующие группы: а) по методу формования: для ручного формования для вакуумной инжекции для горячего прессования для процессов намотки для пултрузии б) по области применения: обычные конструкционные химстойкие огнестойкие теплостойкие светопрозрачные
Основные методы изготовления стеклопластиковых изделий 1. Ручное (контактное) формование При этом методе стеклоармирующий материал вручную пропитывается смолой при помощи кисти или валиков. Затем пропитанный стекломат укладывается в форму, где он прикатывается прикаточными валиками. Прикатка осуществляется с целью удаления из ламината воздушных включений и равномерного распределения смолы по всему объему. Отверждение ламината происходит при обычной комнатной температуре, после чего изделие извлекается из формы и подвергается мехобработке (обрезка облоя, высверливание отверстий и т.д.) Применяемые материалы: Смолы: Любые, например эпоксидные, полиэфирные, винилэфирные. Волокна: Любые. Наполнители: Любые, стойкие к используемым смолам. Основные преимущества: Широко используется в течении многих лет. Простота процесса. Недорогие используемые инструменты, если используются смолы, отверждаемые при комнатной температуре. Широкий выбор поставщиков и материалов. Более высокое содержание стеклянного наполнителя и более длинные волокна по сравнению с методом напыления рубленного роввинга. Основные недостатки: Качество смеси смолы и катализатора, качество ламината, содержание стеклообразующего в ламинате очень зависят от квалификации рабочих. Высокая вероятность воздушных включений в ламинате. Малая производительность метода. Вредные условия труда. 2. Метод напыления рубленного роввинга Стеклонить подается в ножи пистолета, где она рубится на короткие волокна. Затем они в воздухе смешиваются с струей смолы и катализатора и наносятся на форму. После нанесения рубленного роввинга, его необходимо прикатать с целью удаления из ламината воздушных включений. Прикатанный материал оставляют отвердевать при обычных атмосферных условиях. Применяемые материалы: Смолы: Прежде всего полиэфирные. Волокна: Только стеклонить в виде роввинга (ровницы). Наполнители: Любые, стойкие к стиролу. Укладываются вручную. Основные преимущества: Широко используется много лет. Быстрый путь нанесения волокна и смолы. Дешевые формы. Основные недостатки: Ламинаты имеют тенденцию быть очень богатыми смолой и поэтому чрезмерно тяжелыми. Присутствуют только короткие волокна, которые ограничивают механические свойства ламината. Смолы должны быть с низкой вязкостью для возможности их напыления. Это приводит к уменьшению их механических свойств и теплостойкости. Вредные условия труда, большое содержаний в воздухе мелких частиц стекла. Качество конечного продукта в основном зависит от мастерства оператора установки. 3. Метод RTM Стеклоармирующий материал укладывается на матрицу в виде заранее заготовленных выкроек. Затем укладывается пуансон, который прижимается к матрице при помощи прижимов. Смола подается в полость формы под рассчитанным давлением. Иногда, для облегчения прохода смолы через материал используется вакуум, который создается внутри формы. Как только смола пропитала весь стекломатериал, инжекцию останавливают и ламинат оставляют в форме до полного отверждения. Отверждение может проходить при обычной или повышенной температурах. Применяемые материалы: Смолы: эпоксидные, полиэфирные, винилэфирные. Волокна: Любые. Желательно использовать специально предназначенные для этого стекломатериалы с проводящим слоем и механически связанными волокнами. Наполнители: Любые стойкие к стиролу, кроме материалов в виде сот. Основные преимущества: Могут быть получены ламинаты с высоким содержанием стекла и с минимальным содержанием пустот. Хорошие условия труда и окружающей среды. Нет большого выброса вредных веществ. Возможно сокращение трудовых затрат и времени на изготовление изделия. Один рабочий может обслуживать одновременно несколько аппаратов, производяших инжекцию. Вся форма изделия имеет глянцевую поверхность. Минимизированы отходы материалов. Основные недостатки: Дорогие и сложные формы. Сложность процесса. Необходимость иметь инжекционное оборудование. 4. Метод пултрузии Волокна подаются от катушечной рамы до ванны со смолой и затем проходят через нагретую фильеру. В фильере убираются излишки смолы, происходит профилирование ламината и отверждение материала. После этого отвержденный профиль автоматически обрезается на необходимые длины. Применяемые материалы. Смолы: Эпоксидная смола, полиэфирная смола, винилэфирная смола. Волокна: Любые. Наполнители: Не используются. Основные преимущества: Это может быть очень быстрый процесс пропитки и отверждения материала. Автоматизированное управление содержанием смолы в ламинате. Недорогие материалы. Хорошие структурные свойства ламинатов, так как профили имеют направленные волокна и высокое содержание стекломатериала. Закрытый процесс пропитки волокна. Основные недостатки: Ограниченная номенклатура изделий. Дорогое оборудование. 5. Метод намотки Этот процесс прежде всего используется для изготовления пустотелых круглых или овальных секционных компонентов, типа труб или резервуаров. Волокна пропускаются через ванну со смолой, затем через натяжные валики, служащие для натяжения волокна и удаления излишков смолы. Волокна наматываются на сердечник с необходимым сечением, угол намотки контролируется отношением скорости движения тележки к скорости вращения. Применяемые материалы: Смолы: Любые. Волокна: Любые, волокна подаются напрямую от рамы для катушек без дополнительного сшивания в ткань. Наполнители: Любые. Основные преимущества: Это может быть очень быстрый и поэтому экономически выгодный метод укладки материала. Регулируемое соотношение смола/стекло. Высокая прочность при малом собственном весе. Неподверженность коррозии и гниению Недорогие материалы Хорошие структурные свойства ламинатов, так как профили имеют направленные волокна и высокое содержание стекломатериала. Основные недостатки: Ограниченная номенклатура изделий. Дорогое оборудование. Волокно трудно точно положить по длине сердечника. Высокие затраты на сердечник для больших изделий. Рельефная лицевая поверхность. 6. Метод RFI (Resin Film Infusion) Сухие ткани выкладываются вместе со слоями полутвердой пленки из смолы. Весь полученный пакет закрывается специальной пленкой. Сначала между пленкой и формой создается вакуум, после чего форму помещают в термошкаф или автоклав. Под воздействием температуры смола переходит в текучее состояние и благодаря вакууму пропитывает материал. После некоторого времени смола полимеризуется. Применяемые материалы: Смолы: Только эпоксидная смола. Волокна: Любые. Наполнители: Почти все, хотя ПВХ пена нуждается в специальной обработке из-за высоких температур процесса. Основные преимущества: Могут быть получены ламинаты с высоким содержанием стекла и с минимальным содержанием пустот. Высокие физико-механические характеристики из-за твердого начального состояния полимера и высоких температур отверждения. Более низкая стоимость процесса по сравнению с методом препрегов. Хорошие условия труда и окружающей среды. Нет большого выброса вредных веществ. Основные недостатки: Мало применяется вне аэрокосмической промышленности. Для процесса необходима система вакуумного мешка, термошкаф или автоклав. Требования к оборудованию и инструменту по температуростойкости. 7. Метод препрегов Препрег — предварительно пропитанная смолами стеклоткань. Ткани и волокна предварительно пропитаны пред-катализированной смолой под высокой температурой и давлением. В таком виде препреги могут хранится до нескольких недель, однако для увеличения срока хранения, их хранят при пониженных температурах. Смола в препрегах находится в полутвердом состоянии. При формовании препреги укладываются на поверхность формы и закрываются вакуумным мешком. Затем происходит их нагревание до температуры примерно 120 — 180 град.C при этой температуре смола переходит в текучие состояние и препрег принимает размеры формы. Далее при дальнейшем повышении температуры происходит отверждение смолы. Дополнительное давление (до 5 атмосфер) для формования обычно обеспечивается автоклавом. Применяемые материалы: Смолы: Эпоксидные, полиэфирные, фенольные и высокотемпературные смолы типа полиимидных др. Волокна: Любые. Наполнители: Любые стойкие к температурам процесса. Основные преимущества: Могут быть получены ламинаты с высоким содержанием стекла и с минимальным содержанием пустот. Хорошие условия труда и окружающая среда. Нет большого выброса вредных веществ. Возможность автоматизировать процесс и снизить трудовые затраты. Основные недостатки: Высокая стоимость материалов. Для отверждения необходимы автоклавы, которые ограничивают размеры выпускаемых изделий. Контрольные вопросы: 1. Дайте определение композитов. 2. Пенопласты и их основные характеристики. 3. Стеклопластики и их свойства. 4. Способы получения стеклопластиков.
5. Из чего изготавливаю волокна волокнистых композитов? 6. Где, как и для чего применяют композиционные материалы? 7. В чем преимущество композиционных материалов перед металлическими сплавами?. 8.Составить таблицу или схему по классификации композиционных материалов. 9.Описать свойства композиционных материалов.
.
Литература
1. Адаскин А. М. Материаловедение (металлообработка): учеб.пособие для студ. учреждений сред проф. образования/ А. М. Адаскин, В. М. Зуев. – 1-е изд., стер. – М.: Издательский центр «Академия», 2016. – 288 с.
2. Соколова Е. Н. Материаловедение: лабораторный практикум: учеб. Пособие для студ. Учреждений сред. Проф. Образования/ Е. Н. Соколова, А. О. Барышева, А. В. Давыденко. – 2- изд., стер. – М.: Издательский центр «Академия», 2017. – 128 с.
3. Стуканов, В. А. Материаловедение: Учебное пособие/Стуканов В. А. - Москва: ИД ФОРУМ, НИЦ ИНФРА-М, 2015. - 368 с. (Профессиональное образование) ISBN 978-5-8199-0352-0.: - URL: https://znanium.com/catalog/product/508597 - Текст: электронный.
4. https://the-distance.ru/prakticheskaya-rabota-1-vidy-kompozicionnyx-materialov-vgau/
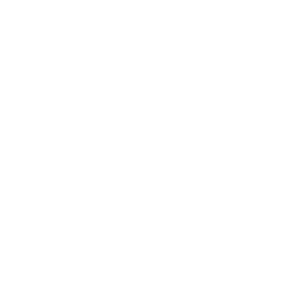
Начало формы
|